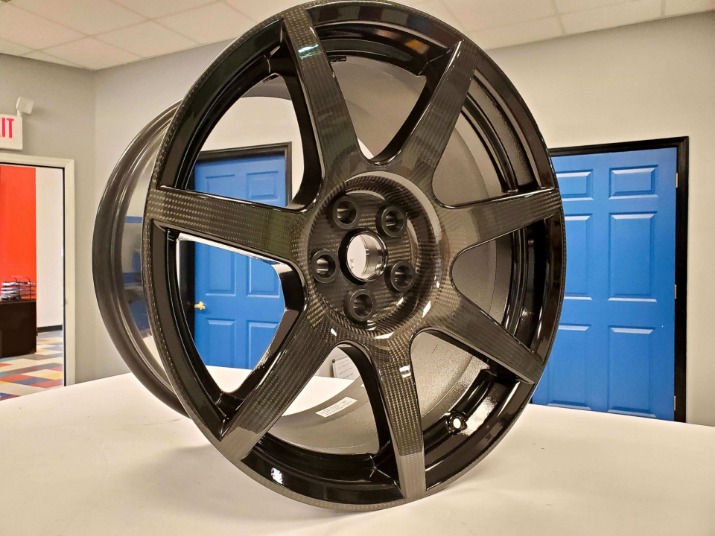
If you’re running a script or application, please register or sign in with your developer credentials here. Additionally make sure your User-Agent is not empty and is something unique and descriptive and try again. If you’re supplying an alternate User-Agent string,try changing back to default as that can sometimes result in a block. Here is a timelapse of my 3rd Layup, maybe I will do a video later where I closely show the process of the Layup… After curing for about 12hours at Room-temperature I put my parts into a foam oven and slowly increase the temperature to about 40-45degC for about 10 hours.
Read more about golf black badges here.
Here are some shop in the USA that sell carbon fiber car parts:
They can achieve complicated mold shapes with fine details that would be difficult to manufacture with traditional methods. Our production processes include injection moulding, carbon fibre prepreg component manufacture and composite compression moulding supported by primer and top coat paint lines to give you a complete production solution. Many car performance enthusiasts, who cannot afford a luxury CFRP bodywork car, have the option of upgrading their vehicles with carbon fibre car parts. There is one type that enjoys extreme popularity, despite its rather high price. One of the biggest concerns with carbon fiber is its high raw material cost.
You can also have fiber car wraps installed on your hood, spoiler, mirrors, or anywhere else to improve the look of your car. Knowing the properties of the material of your car parts is beneficial. It’ll also help you avoid unnecessary maintenance costs and physical damage to the car. In a vehicle, you travel with your loved ones and family, which makes it even more important to ensure that the vehicle parts are in good condition and of good material. Carbon fiber provides a perfect pocket and effort-saving option and is also a good option to extend the life of your vehicle. The film produced initially is very thin and can be modified for the size needed.
Step 2: Apply a Layer of Wax
We recommend using carbide tools, abrasive type cutters, or diamond-crusted blades. Regular steel tools will do the job, but carbon fiber’s strength and abrasiveness will wear down standard tools quickly. Once your piece is cut, you can sand the edges very lightly with 220 grit sandpaper for a smooth, clean edge. It is applied layer by layer, the first layer being attached to the mild with a specially designed spray adhesive, which is subsequently absorbed by the resin. It is extremely important that the first layer lies tightly in the shape of the mold and the texture of the fabric is beautifully arranged. Each subsequent layer of carbon fabric is laid on top of the previous one, fixing it again with spray glue.
Arranged in this way, the mold is ready for closing with vacuum foil, which is glued along the edge of the mold to the initially placed butyl double-sided tape. The Formula Student team of TU Berlin (FaSTTUBe) manufactured a dozen of carbon fiber parts for racing cars. Engineers in the team hand laminate on a mold directly printed with Formlabs Tough 1500 Resin. This resin is characterized by a tensile modulus of 1.5 GPa and elongation at break of 51%. It is not only strong and supportive during the layup but also sufficiently flexible to separate the part from the mold after curing. Plies are then cured into the mold under heat and pressure in an autoclave. This is a more precise and repeatable process because the quantity of resin is controlled but it is also the most expensive technique that is usually used in high-performance applications.
Value (Versus Cost) of Carbon Fiber is Great
With our optimized production processes, we ensure quick delivery and high quality. We have the ability to produce both in small as well as in larger series.
This process is completed over the original panel / component for that perfect fit and finish. The latest development in carbon fiber technology is tiny carbon tubes called nanotubes. Another characteristic is that they are highly chemically resistant and have a high-temperature tolerance with low thermal expansion. Once happy with placement, a protective layer of bagging film is used and a lot of weights are applied to hold the skins together properly while they cure. Using a Dremel style cutting tool fitted with a Perma-Grit cutting wheel, the edge of the lower skin was then roughly trimmed. Carbon Fibre vs Glass FibreCarbon fibre is more than 20 percent stronger than the best fibreglass.